Controls
Part 1
Refrigeration systems require operating controls so they can cycle on and off to maintain a certain temperature. They also require safety controls to stop operation if unsafe conditions occur. There are many varieties of controls. Different types respond to temperature, pressure, humidity, liquid levels, other controls, manual intervention and other things.
Thermostatic Control
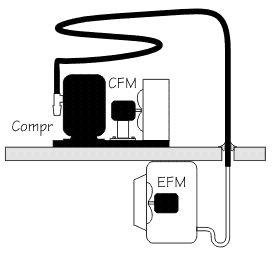
Lets add a basic control system to a refrigeration system. First we need to know what loads there are to be controlled. The image on the left shows a small split system for a walk in cooler with 3 electrical devices; a compressor, condenser fan motor and evaporator fan motor. Those 3 electrical devices are represented on the ladder schematic shown below. This type of wiring diagram has branch runs all shown as parallel circuits going from the left line (L1) to the neutral line (N). They look like the rungs in a ladder hence the name ladder schematic. The EFM (Evaporator Fan Motor) must run all the time so that the box temperature stays uniform and the thermostat senses the average box temperature not some pocket of stratified air. Press the Off Cycle Button to see the circuit through the EFM. Now Press the On Cycle Button to close the T-STAT (thermostat) and call for refrigeration. The T-Stat "makes" on a rise of temperature. Notice that the COMPR (compressor) and the CFM (Condenser Fan Motor) both come on. A T-Stat that "makes on a rise" is a cooling T-Stat. A T-Stat that "makes on a fall" is a heating T-Stat.

Also note that just because the wiring on the left side of the T-Stat is not coloured red when the T-Stat is open, that does not mean there is no electricity there. There is a full electrical potential on that line and if you were to come along and stick your finger at that point you would be shocked. The red coloured wiring indicates the logical flow routes. Non red wires are not necessarily without voltage potential.
The graph below shows how an operating control cycles. The control is set to start refrigeration if the box warms up to 40 °F That's called the Cut In point. The system keeps running until it reaches the Cut Out point which is 37 °F where it shuts off and awaits the next call for cooling. In this example there is a 3 °F differential between the cut in and cut out points. The differential must be wide enough that the equipment does not short cycle. Short cycling means to turn on and off too rapidly. Starting is hard on the equipment, so you want to keep the number of starts per hour to a reasonable amount, not an excessive amount. The 40 °F point is a very special temperature. It is the standard cut in point for most refrigeration systems. Above 40 °F bacterial growth rates in stored food increase dramatically. Below 40 °F bacteria growth rate is subdued.
The cut out point is more of a compromise than anything else. Some products may store better at colder temperatures but colder temperatures might adversely affect other products in the same box. There is also a concern about keeping the evaporator from icing up. There is no active defrost system in a standard refrigeration system. (defrost systems are only a standard item with freezers) If a refrigeration system was set to cut in at 36 °F and cut out at 33 °F and the evaporator was operating with a 7 °F TD to the box air, the temperature of the evaporator fins would be 29 °F to 26 °F during the run cycle. Since the freezing point of water is 32 °F you can see that moisture in the air would sublimate onto the evaporator surface and grow into thicker and thicker layers of ice. Not only does ice act like an insulator and reduce thermal transfer, it can totally block airflow through the evaporator fins and virtually stop thermal transfer. Some people try to push this wall a little and it is possible to squeak out a degree or 2 colder than a 40 °F cut in point. However, anything more than a couple of degrees will risk icing the evaporator.
A countering force is the "off cycle defrost" effect. Since a typical refrigerator is designed to maintain 40 °F the recirculating air will tend to melt ice build up on the evaporator during the times it has it has cycled off. There are of course refrigeration systems that are designed to operate in the 35 °F (and colder) range. However these typically have some form of defrost system. Systems that are designed to operate below 32 °F are freezers with defrost systems and they typically operate in temperature ranges like: 0 °F, -10 °F,and -15 °F as well as much colder.

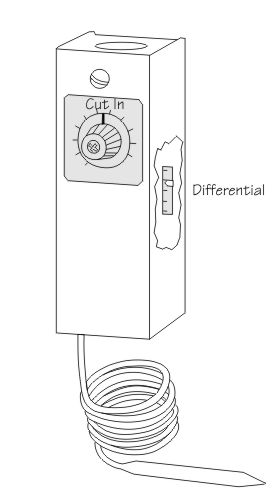
The adjustment knob on a commercial T-Stat sets the cut in point. The differential is adjustable by setting a slider inside the enclosure. Thermostatic controls are manufactured with an wide range of variations. They have fixed differentials, adjustable differentials, different operating ranges and various accuracy's, various electrical load ratings, different types of sensors, electro-mechanical, electronic etc.

The sensing bulb of the control should be mounted so that it senses the evaporator inlet air. During the off cycle the constant fan recirculates the air in the box. The temperature of the air becomes an average of the product temperature, the wall temperature, any infiltrated air and any other loads such as caused by a person entering the box. When the air temperature reaches the cut in point of the control it brings on refrigeration.
When refrigeration is operating, 40 °F air passes through the evaporator and drops in temperature several degrees. That's why the sensor can not be placed in or near the discharge air stream. If it was placed there, the control would think that the whole box was cold and shut off the system as soon as it started. It is the average box temperature that should be monitored, not the discharge air temperature.
Some thermostatic controls are designed with a capillary line temperature sensor which is intended to be inserted between the evaporator fins on units that have a tendency to ice up. A commercial cooler in a hot environment which is constantly being accessed would tend to ice up. A Constant Cut In Control, also known as a beverage cooler control, forces an off cycle defrost at the end of each run cycle. The control will remain open until the evaporator has reached a temperature which indicates that any frost accumulated during the previous run cycle has been melted. This type of control is used in appliances like beverage coolers. Adjusting the knob on this type of control changes only the Cut Out setting, the Cut In setting remains fixed.